A Comprehensive Guide to Gas Turbine Combustion in Steam Engine Generators
Gas turbine combustion plays a crucial role in the operation of steam engine generators. These generators are widely used in power plants, industrial facilities, and even on ships, providing a reliable and efficient source of electricity.
Understanding the combustion process in gas turbines is essential for optimizing their performance and reducing emissions.
In this comprehensive guide, we will explore the key concepts and principles of gas turbine combustion, including the types of fuels used, the combustion process, and the factors that influence combustion efficiency. So let’s dive in!
1. Types of Fuels Used in Gas Turbine Combustion
Gas turbine combustion can be fueled by various types of fuels, depending on availability, cost, and environmental considerations. The most common fuels used in gas turbine combustion include natural gas, diesel, and kerosene. Natural gas is the cleanest and most environmentally friendly fuel, as it produces lower emissions of pollutants such as sulfur dioxide and nitrogen oxides. Diesel and kerosene are typically used in situations where natural gas is not available or as a backup fuel.
2. The Combustion Process in Gas Turbine Combustion
The combustion process in gas turbine combustion involves the mixing of fuel and air, followed by ignition and combustion. The primary components of the combustion process include the fuel injection system, the combustion chamber, and the flame stabilization mechanism. Let’s take a closer look at each of these components:
3. Factors Affecting Combustion Efficiency
Several factors can influence the combustion efficiency in gas turbine combustion. These factors include the air-fuel ratio, combustion temperature, and the presence of impurities in the fuel. Let’s explore each factor in more detail:
1. Air-Fuel Ratio: The air-fuel ratio refers to the proportion of air to fuel in the combustion process. It is crucial to maintain the proper balance to achieve optimal combustion efficiency. When the air-fuel ratio is too high (lean mixture), there is excess air, which can result in incomplete combustion. On the other hand, if the ratio is too low (rich mixture), there is excess fuel, leading to inefficient combustion and the production of harmful emissions.
2. Combustion Temperature: The combustion temperature is another important factor influencing combustion efficiency. A higher temperature generally implies more complete combustion and better efficiency. However, there is a limit to the temperature due to the potential formation of nitrogen oxides (NOx) – a harmful pollutant. Therefore, it is essential to carefully control and optimize the combustion temperature to strike a balance between efficiency and emissions.
3. Presence of Impurities in the Fuel: The presence of impurities in the fuel can have a significant impact on combustion efficiency. These impurities can vary widely, including sulfur, heavy metals, and contaminants. They can negatively affect the combustion process by interfering with the combustion chemistry and catalysts present in the gas turbine. Impurities can lead to fouling, corrosion, and increased emissions. Therefore, it is crucial to ensure fuel quality standards and employ proper filtration and treatment methods to minimize the adverse effects of impurities.
In summary, maintaining the correct air-fuel ratio, controlling the combustion temperature, and addressing fuel impurities are all essential for optimizing combustion efficiency in gas turbines. By carefully managing these factors, operators can achieve improved efficiency, reduced emissions, and enhanced overall performance.
4. Emissions Control in Gas Turbine Combustion
Emissions control is a critical aspect of gas turbine combustion to comply with environmental regulations and reduce the impact on air quality. The primary emissions of concern in gas turbine combustion are nitrogen oxides (NOx), carbon monoxide (CO), sulfur dioxide (SO2), and particulate matter. Let’s discuss some of the common techniques used for emissions control:
1. Lean Premixed Combustion: This technique involves injecting a carefully controlled amount of air into the combustion chamber to create a lean fuel-air mixture. By reducing the amount of fuel available for combustion, the formation of nitrogen oxides is minimized.
2. Water or Steam Injection: Water or steam can be injected into the combustion chamber to lower the flame temperature and reduce the production of nitrogen oxides. This technique is known as wet or steam injection and can be particularly effective in reducing NOx emissions.
3. Selective Catalytic Reduction (SCR): SCR is a post-combustion technique that involves injecting a reductant, such as ammonia or urea, into the exhaust stream. The exhaust gases then pass through a catalyst bed, where nitrogen oxides are converted into harmless nitrogen and water.
4. Dry Low NOx (DLN) Combustion: DLN combustion systems are designed to reduce nitrogen oxide emissions by optimizing the combustion process. This can be achieved by using advanced fuel injection techniques, such as staged or lean-premixed combustion, as well as advanced combustion controls.
5. Flue Gas Desulfurization (FGD): FGD is a technique used to remove sulfur dioxide from the exhaust gases of a gas turbine. This can be done through various methods, such as wet scrubbing or dry sorbent injection, which involve the use of chemicals to react with and remove sulfur dioxide.
6. Particulate Matter Control: To control particulate matter emissions, gas turbines may be equipped with filters or electrostatic precipitators to capture and remove particulates from the exhaust gases. These devices operate by either physical filtration or electrostatic attraction.
It is important to note that different gas turbine models and applications may require specific combinations of these techniques or additional emissions control measures to meet regulatory requirements and achieve desired emission reduction goals.
5. Future Trends in Gas Turbine Combustion
The field of gas turbine combustion continues to evolve, driven by the need for higher efficiency and lower emissions. Here are some of the future trends and advancements in gas turbine combustion:
1. Lean premixed combustion: Lean premixed combustion is a technique that involves mixing the fuel and air in a lean mixture before combustion. This results in lower emissions of nitrogen oxides (NOx), which are a major contributor to air pollution. Researchers are continuously working on developing more efficient and reliable lean premixed combustion systems for gas turbines.
2. Hydrogen combustion: With the increasing demand for clean and renewable energy sources, hydrogen has gained attention as a potential fuel for gas turbines. Hydrogen combustion produces only water vapor as a byproduct, making it a carbon-neutral option. However, there are challenges associated with storing and handling hydrogen, as well as ensuring safe and efficient combustion. Ongoing research is focused on overcoming these challenges and exploring the potential of hydrogen as a fuel for gas turbine combustion.
3. Multi-fuel capability: Gas turbines are being designed with the ability to burn a wide range of fuels, including natural gas, syngas, biofuels, and even waste gases. This multi-fuel capability allows for greater flexibility in fuel choice, which can help reduce dependence on a single fuel source and increase resilience in energy systems. Advances in fuel flexibility are being made through improved combustion control and the development of advanced fuel injection systems.
4. Advanced combustion modeling: Computational fluid dynamics (CFD) modeling is being used extensively in the design and optimization of gas turbine combustion systems. Advanced combustion models can accurately predict flow patterns, heat transfer, and pollutant formation within the combustion chamber. These models help engineers optimize combustion efficiency, reduce emissions, and improve the overall performance of gas turbines.
5. Active combustion control: Active combustion control techniques involve using sensors and actuators to dynamically adjust the combustion process in real-time. By continuously monitoring combustion conditions and making adjustments, active combustion control can optimize fuel-air mixing, reduce emissions, and enhance combustion stability. This technology is being actively researched and implemented in gas turbine combustion systems.
6. Additive manufacturing: Additive manufacturing, or 3D printing, is revolutionizing the manufacturing process for gas turbine components. By using additive manufacturing techniques, intricate and complex geometries can be created, which can enhance combustion efficiency and reduce emissions. This technology also allows for rapid prototyping and customization of components, leading to faster innovation and improved performance in gas turbine combustion systems.
Overall, the future of gas turbine combustion is focused on achieving higher efficiency, lower emissions, and greater fuel flexibility. Advances in lean premixed combustion, hydrogen combustion, multi-fuel capability, combustion modeling, active combustion control, and additive manufacturing are driving these advancements and shaping the future of the field.
Conclusion
Gas turbine combustion in steam engine generators is a complex process that involves the careful management of fuel and air to achieve efficient and clean combustion.
By understanding the different components of the combustion system and the factors that affect combustion efficiency, operators can optimize their gas turbines for maximum performance and minimal emissions.
As the need for cleaner and more sustainable energy grows, advancements in gas turbine combustion technologies will continue to drive the industry forward, enabling us to meet our energy demands while minimizing our environmental impact.
You May Also Like
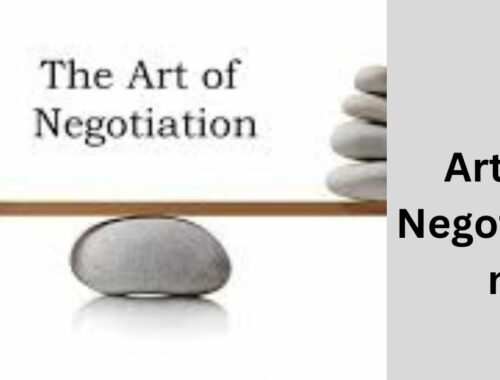
The Art of Negotiation: Navigating the Deal or No Deal Dilemma
January 2, 2024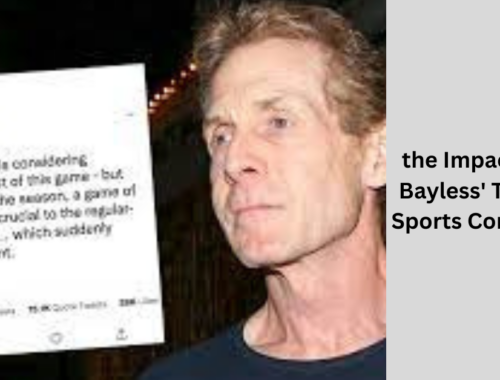
Analyzing the Impact of Skip Bayless’ Tweets on Sports Commentary
February 2, 2024